Formosa Laboratories 2022 Material Topic: Occupational Safety and Health
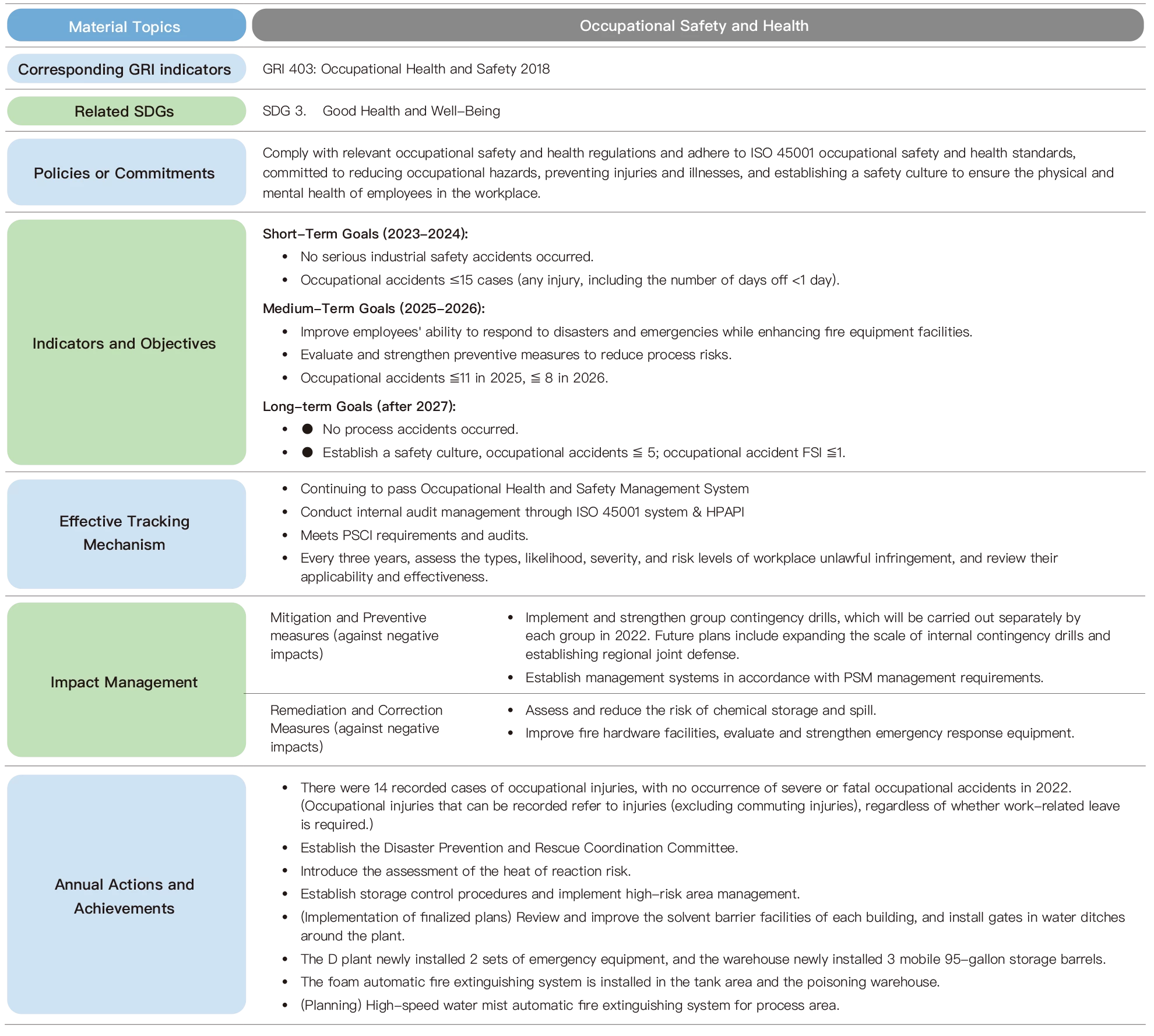
Occupational Health and Safety Management System
To maintain employee safety and prevent occupational accidents, the Company implements occupational safety management based on the ISO 45001 Occupational Health and Safety Management System. The scope of the occupational health and safety management system covers the Formosa Laboratories Louchu Plant and Louchu Plant 2, regulating all workers and production activities of custom synthesis and mass production of APIs and specialty chemicals at these workplaces, ensuring coverage at a rate of 100%. In accordance with the Occupational Safety and Health Act and related laws and regulations, we have established an "Occupational Safety and Health Management Program" comprising sixteen major items, and formulated various work objectives, schedules, and measures, using the PDCA (Plan-Do-Check-Act) cycle for quality management. The program aims to continuously assess occupational hazards and improve the occupational health and safety management system. We have also established occupational safety and health units, management personnel, and emergency medical personnel in compliance with the law to prevent workplace accidents comprehensively.
Formosa Laboratories' 16 Major Items of Occupational Safety and Health Management Program
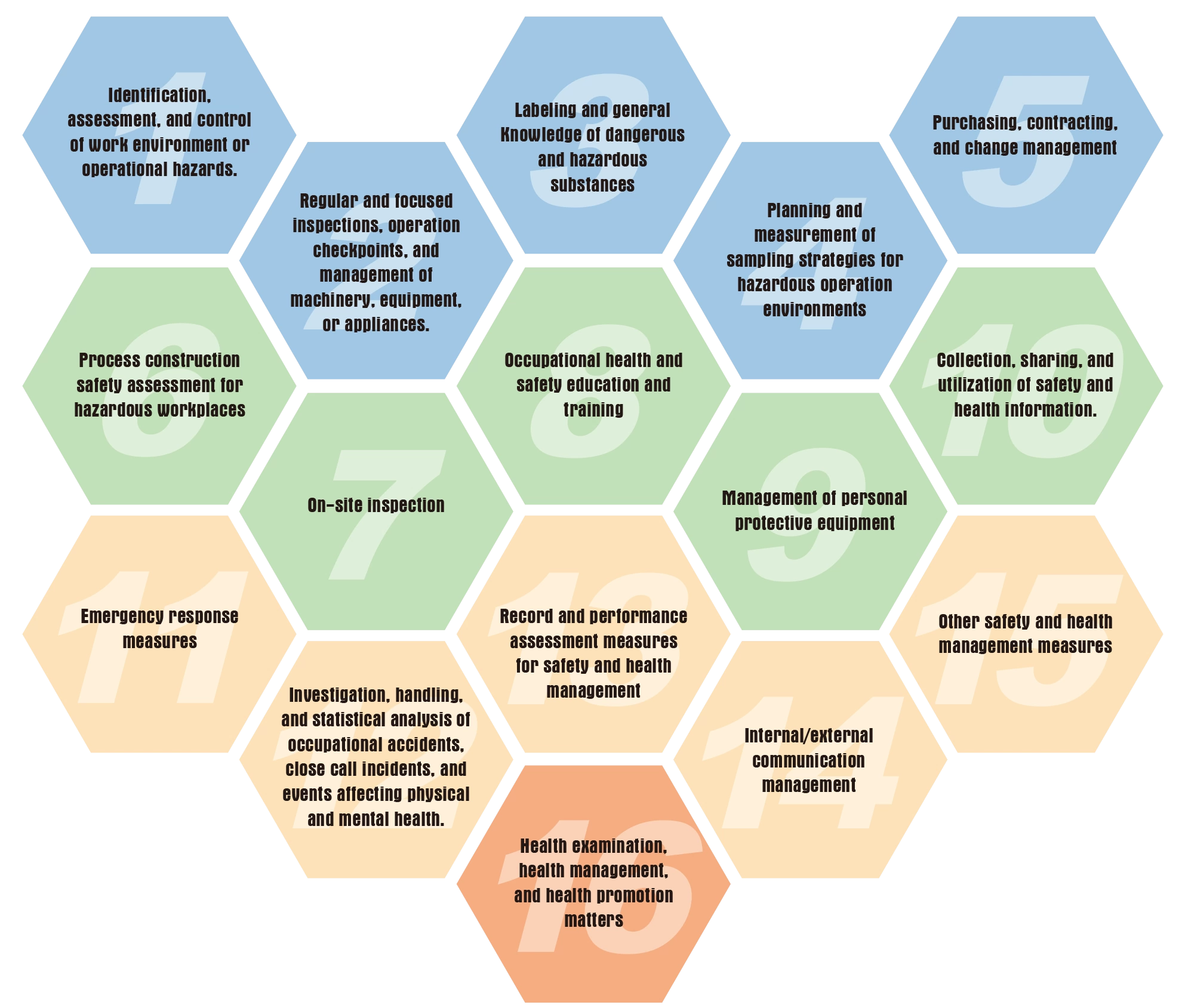
Occupational Safety and Health Committee
To protect the rights and interests of employees, the Company has established an Occupational Safety and Health Committee in accordance with the requirements of the "Regulations on Occupational Safety and Health Management", which is composed of the occupational safety and health unit, the first-level supervisors of each department, and the labor representatives of the labor-management meeting. The Committee comprises a total of 20 members, including 1 medical personnel, 1 occupational safety and health personnel, 11 supervisory and commanding personnel from each department, and 7 labor representatives. The labor representatives make up more than one-third of the total.
The Occupational Safety and Health Committee is responsible for improving the occupational safety and health environment, enhancing the level of safety and health management, and achieving safety management goals through planning, implementation, and assessment. A safety and health committee meeting is held quarterly to discuss topics including the management of occupational accidents, education training and campaign, environmental monitoring reports, employee health protection and health monitoring analysis, implementation results of health promotion, fire alarm management, emergency response management, safety and health management of contracted businesses, automatic inspection management, audit inspections, application for the operation of toxic chemicals operation and management of controlled chemicals registration, safety and health self-evaluation management, and management review reports of occupational safety and health management systems.
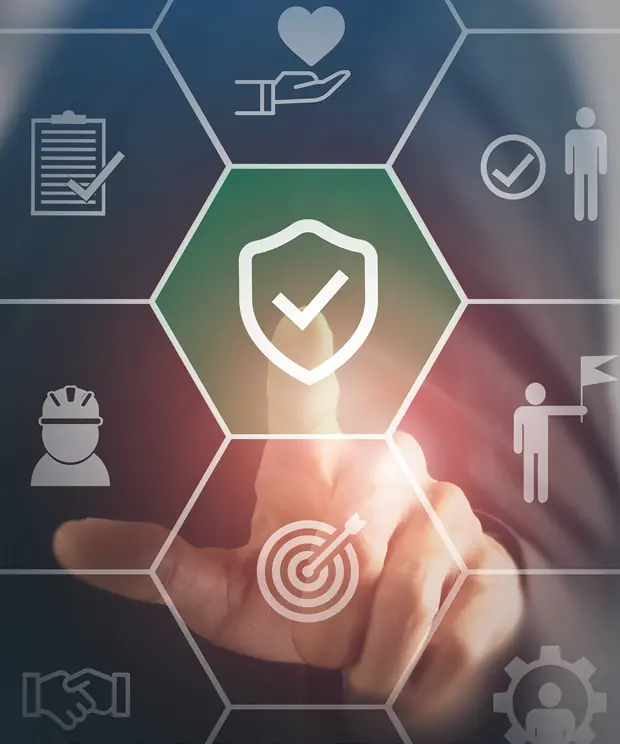
Occupational Health and Safety Education and Training
To ensure a safe and healthy work environment for employees, the Company implements emergency response measures such as emergency equipment preparation, emergency response personnel training, preparation of off-site emergency response centers, preparation of off-site emergency evacuation and shelter locations, emergency response drills, earthquake response procedures, chemical spill handling procedures, and typhoon response. Additionally, we regularly conduct occupational safety training for new employees and contracted workers, as well as refresher training for existing employees, to ensure that employees can learn the necessary safety knowledge for their work.
Special training for units and engineers operating and using chemicals with higher potential risks has been completed for the year 2022. New employees have also achieved a 100% completion rate for general occupational safety and health education training. To prevent similar accidents from recurring, Formosa Laboratories also conducts regular accident education training, sharing industrial safety incident cases to help employees understand the true causes of accidents, reduce industrial accidents, and enhance employee health and safety.
Personnel Occupational Health and Safety Training 2022
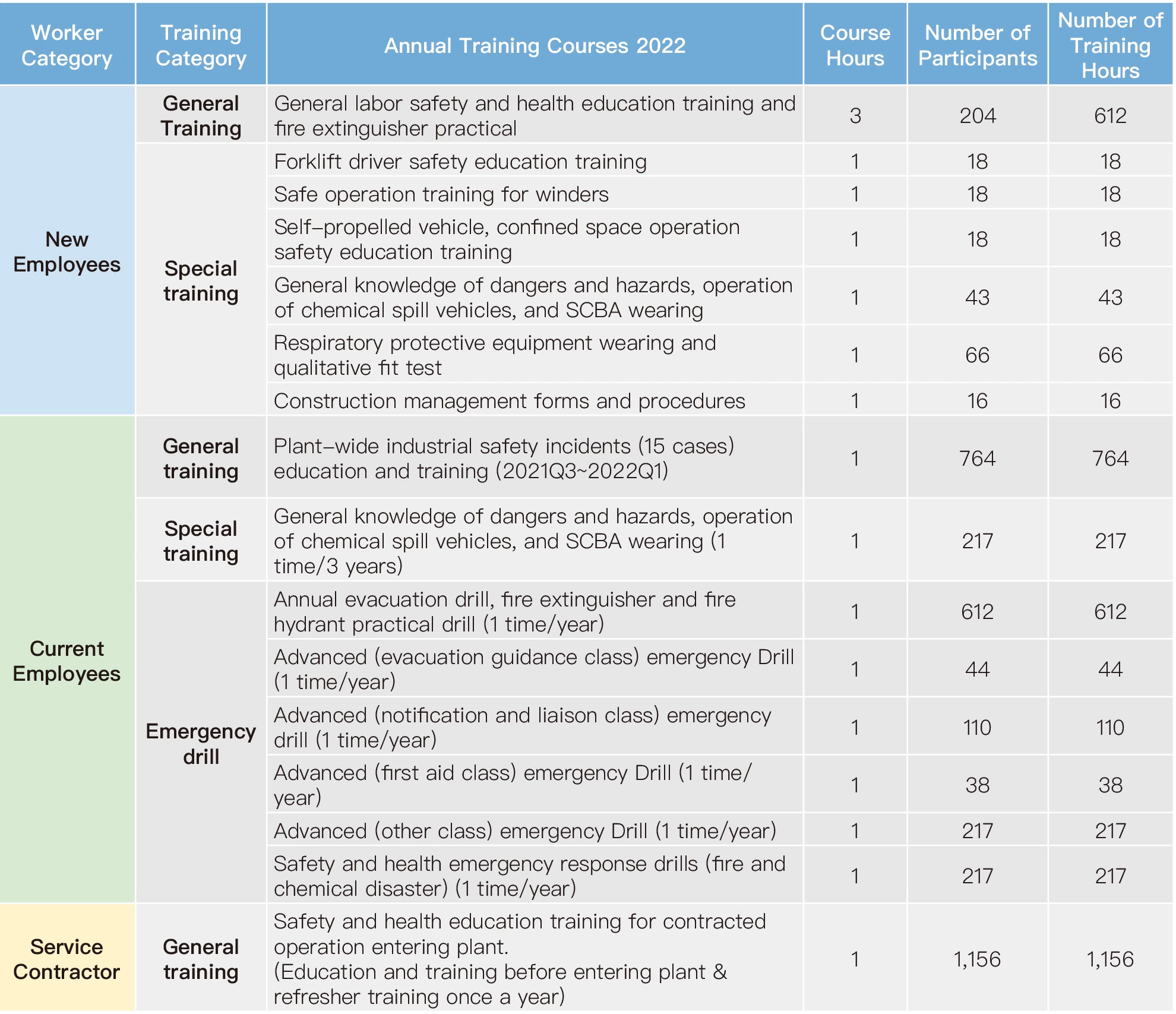
Occupational Hazard Risk Management
Based on the record of occupational accident incidents, the Company assists various units in conducting hazard identification and risk assessment to establish risk levels. Currently, the highest potential risk is the physical hazard generated by noise operations. In addition to strengthening education and training and providing protective equipment, we also track employees' physical health through regular health examination to control and prevent occupational diseases. For other potential hazards in the process of process operations, including improper injury from mechanical operations and hazards from chemical use, we also enhance relevant special education and training for designated operating units and engineering personnel, setting management goals and tracking regularly. For example, we arrange advanced emergency drills, fire, and chemical disaster response drills once a year. Also, we annually review and update the timing table for the use of protective equipment. The timing table is used as a guide for wearing appropriate protective equipment to conduct automatic mechanical equipment inspections and manage hazardous mechanical equipment to continuously ensure the effectiveness of protective measures.
Hazard Identification, Analysis, Prevention, and improvement measures in the Occupational Safety and Health Management of Formosa Laboratories.
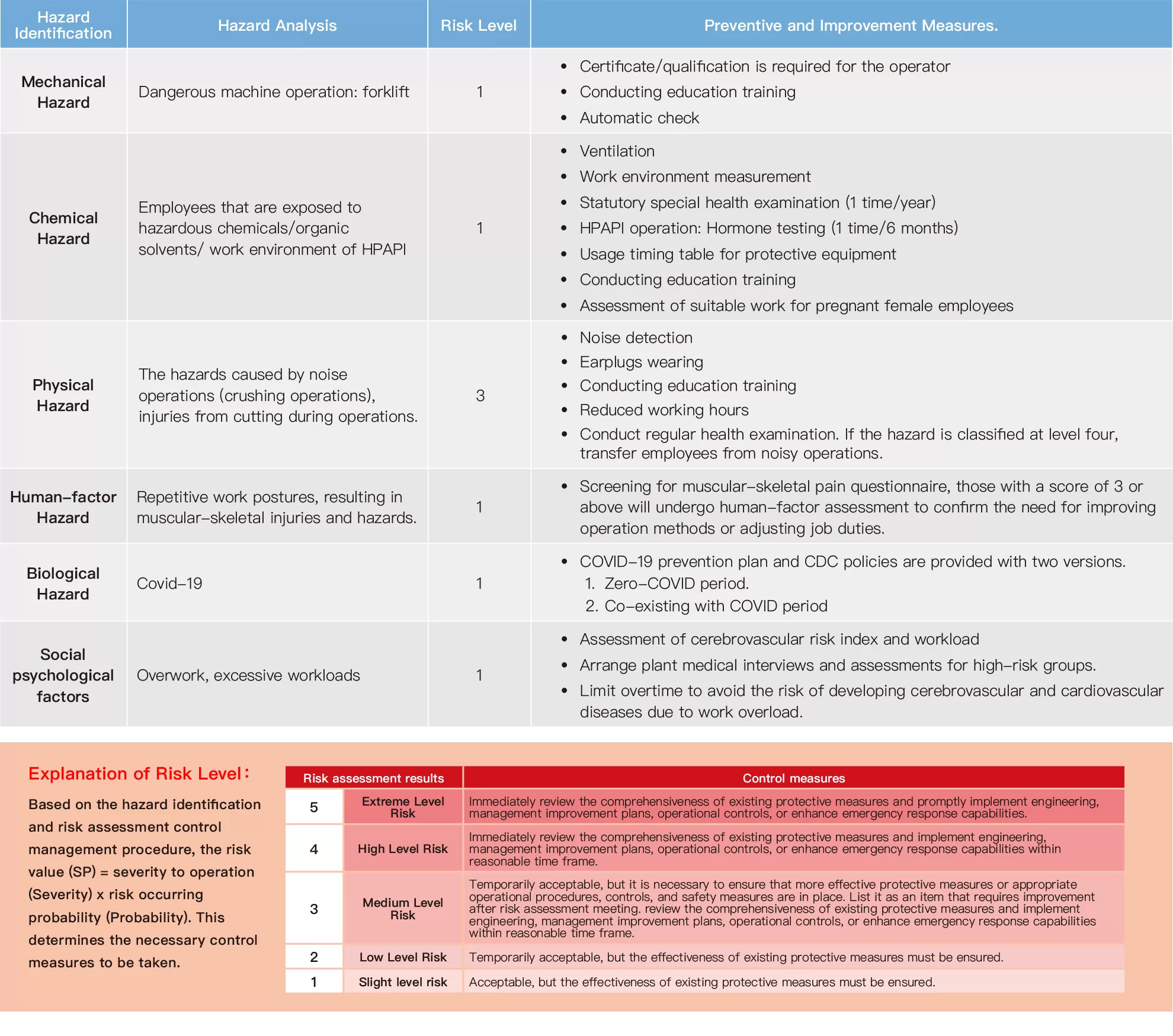
Hazardous Substance Management
Formosa Laboratories has established a hazardous substance process management system to mitigate the impact of hazardous substances on the environment and society and prioritize the health and safety of employees. The operation involves verifying the storage of raw materials, reviewing the part number of finished products, assessing whether they comply with applicable regulations regarding chemicals, and conducting classification. A chemical list is established, including raw materials, miscellaneous items, and finished products, and systematic management and control are carried out in accordance with the different chemical hazard risks and legal requirements. In addition to setting up local exhaust devices, a personal protective equipment usage schedule is established based on the results of risk assessments for each unit to reduce direct contact between personnel and chemicals or hazards that may cause injuries to various parts of the body.
This serves as a basis for employees to follow, and to enhance the implementation of wearing personal protective equipment.
The Company conducts hazard awareness education and refresher training every 3 years in order to carry out effective management of hazardous substances health and safety. We update the "List of Pregnancy Hazardous Chemicals Used in Each Plant Area" annually and provide plant nurses and unit supervisors with appropriate work assessments for pregnant female workers. In addition, for health and safety assessments, we propose relevant recommendations and disclosure indicators based on the practice of chemical risk and hazard assessment management in products, including the identification of the number of substances with health hazards or the number of CMR substances.
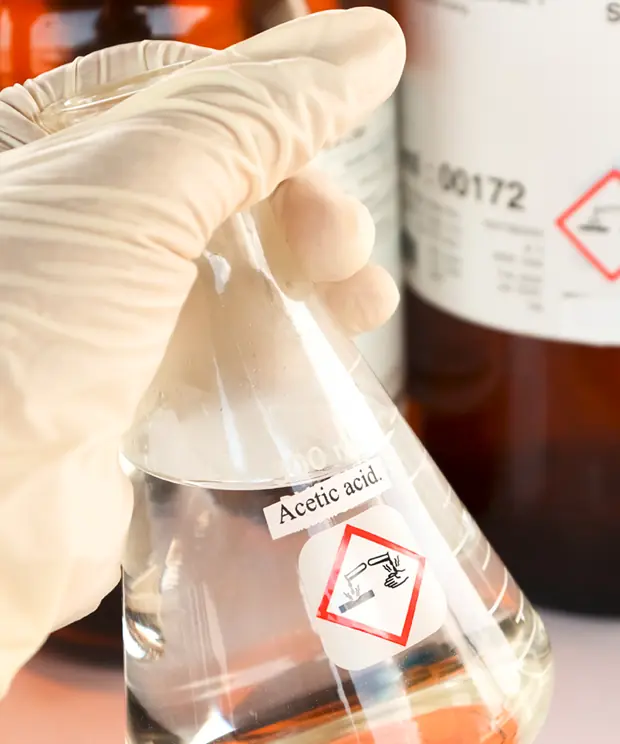
Types of Hazardous Substances Regulated by Formosa Laboratories in 2022
Regulated Characteristics | Type |
---|---|
For chemicals that are hazardous to female workers under the age of 18, as well as those who are pregnant or have given birth within the past year. | 7 |
Substance of carcinogenic, mutagenic or toxic for reproduction, CMR | 42 |
Contractor Occupational Health and Safety Management Measures
Based on the Company's 16 occupational safety and health management plans, we conducted contractor toolbox meetings and organization of agreements, carried out contractor safety audits and imposed penalties for violations, developed contractor emergency response plans, implemented safety permits and hazardous operations measures for contractor, revised contractor safety and health management regulations, and provided contractor safety education and training for onsite entry. The following are the four main areas of control and guide for contractors.
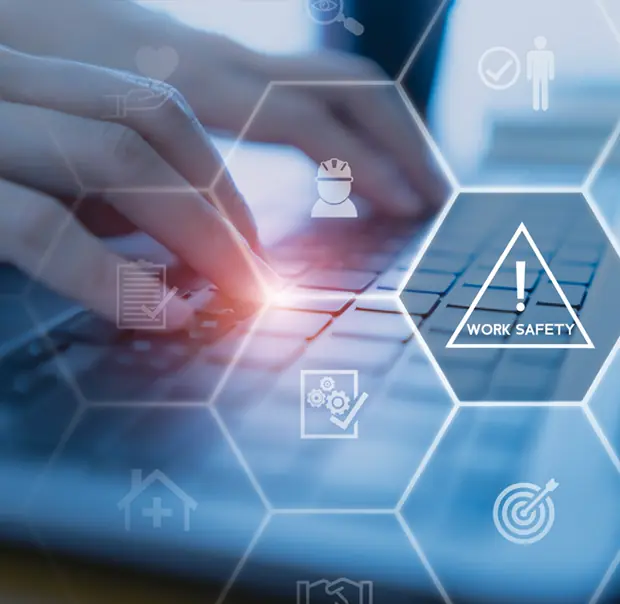
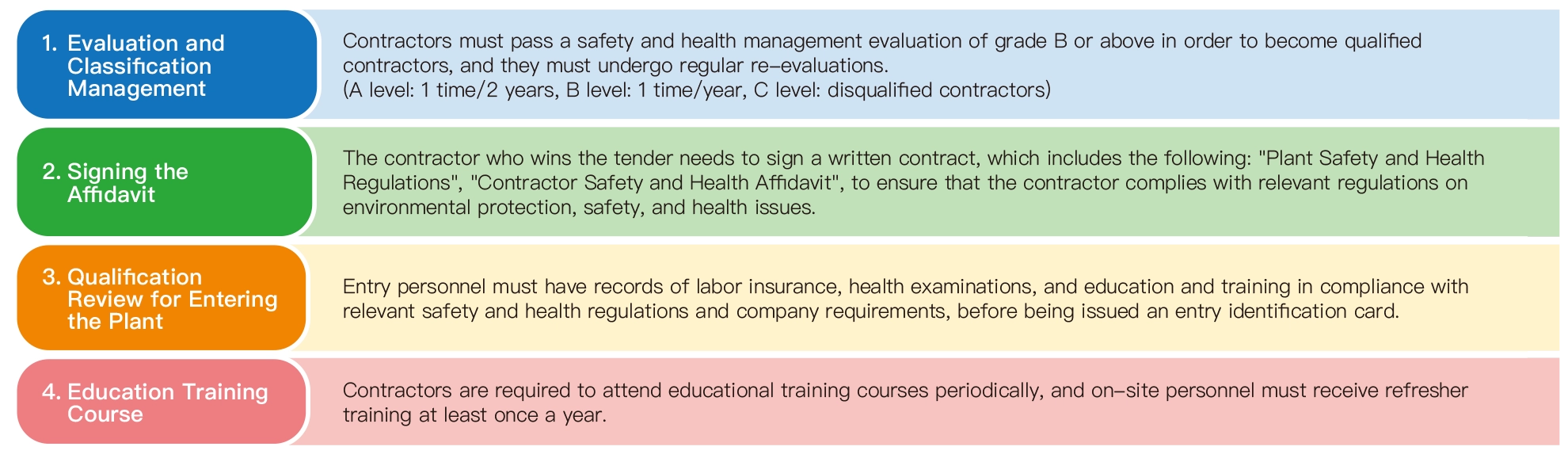
Occupational Accident Emergency Response
Notification and Handling Procedures for Occupational Accidents at Formosa Laboratories
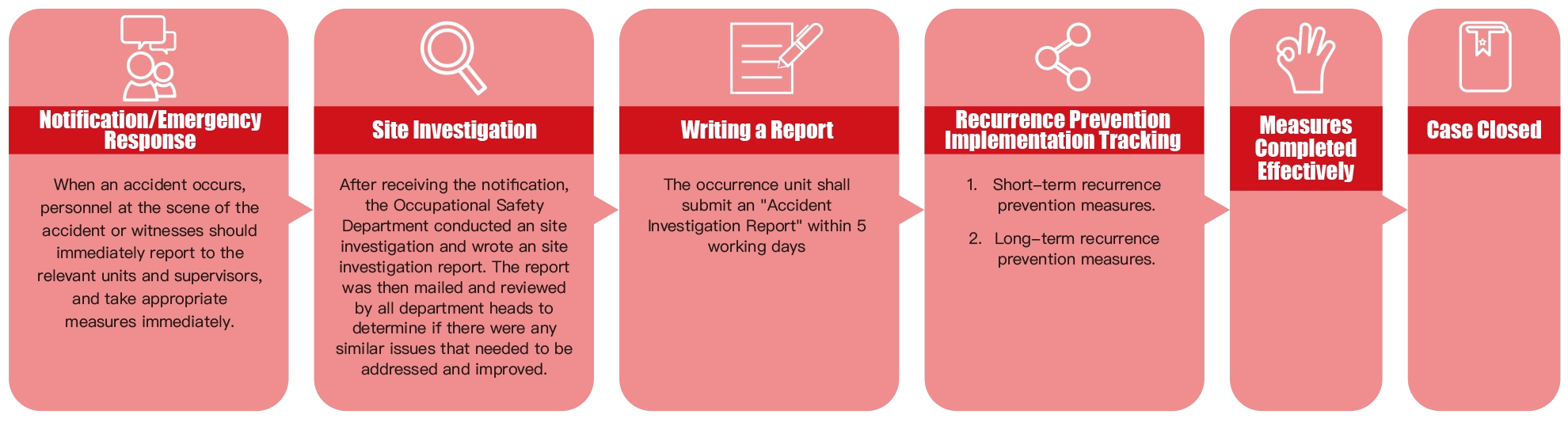
Investigation Procedures for Occupational Accidents at Formosa Laboratories
Accidents Occurrence |
|
---|---|
Investigation of the cause of the incident. |
|
Review and Improvement Measures for the Incident | Proposed by the unit that the accident occurs, monitor and track improvement measures based on the accident investigation and analysis report. These measures shall be implemented until improvements are completed, and a comprehensive review and assessment shall be conducted to prevent similar incidents from happening again. |
Occupational Injury Accident Statistics and Analysis
To protect the rights and interests of laborers and provide a safe and reliable working environment, Formosa Laboratories regularly plans and measures the sampling strategy for hazardous working environments. We implement outsourced environmental monitoring management, self-noise detection management, self-illumination detection management, as well as safety and health equipment and facility management to eliminate occupational hazards and minimize risks. According to the measurements and statistical results, the total working hours of Formosa Laboratories employees in 2022 were 1,685,056 hours, with 14 recorded cases of occupational injuries and no serious occupational injuries or fatal accidents caused by occupational injuries. Analyzing the accident categories for the entire year, the highest number of occupational injuries was caused by hand cuts (6 cases, accounting for 43%), followed by contact with hazardous substances (3 cases, accounting for 21%). In 2023, we will promote the Behavior-Based Safety (BBS) mechanism to establish a safety culture as our goal and continuously enhance the safety monitoring system.
Statistics on Occupational Injuries among Chemical Workers in the Past 3 Years.
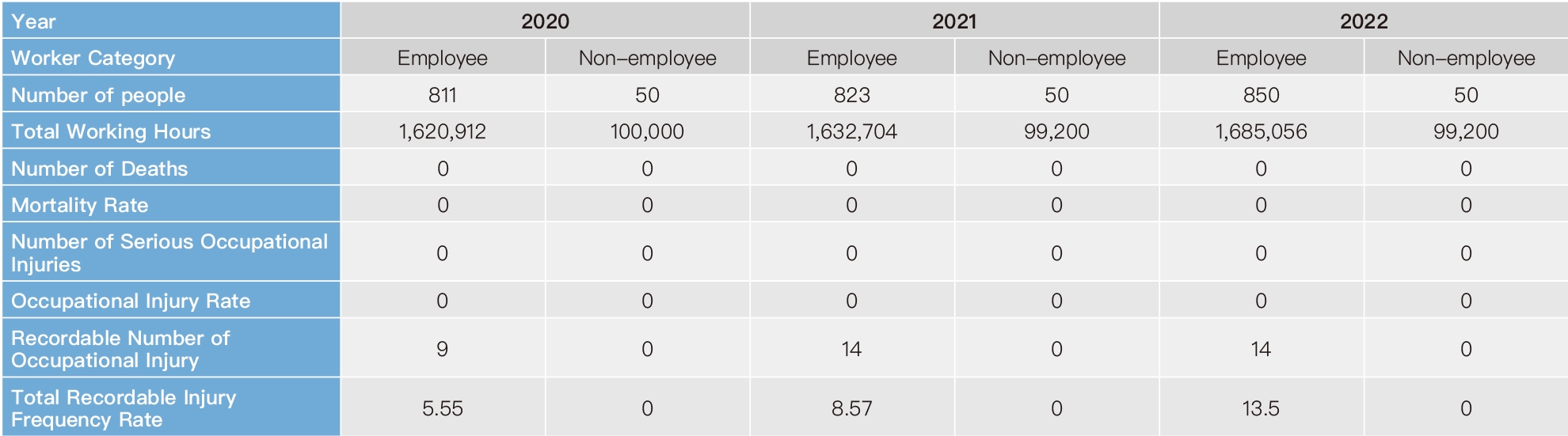

Note:
- Occupational injuries refer to accidental injuries that occur while workers are performing their duties or in the workplace. The statistical criteria do not include commuting accidents to and from work.
- The number of employees is the average of the reported number of occupational accidents each month in that year; the number of non-employees is the sum of dispatched, resident contract personnel, and the average of about 10-30 people per day for general engineering contracts, with a total average of 50 people per month.
- Total working hours: calculate the total annual working hours for all workers; employees' working and overtime hours are calculated based on actual hours worked; non-employees(contractors and dispatched workers) are estimated based on 8 hours per day × an average of 50 people per day × the total number of working days in a year.
- Serious occupational injury: refers to injuries caused by occupational hazards that result in disability or the inability to recover to the pre-injury state of health within 6 months (excluding death).
- Other recordable occupational injuries are defined as injuries (excluding commuting injuries) that are counted whether they require time off from work or not.
- Mortality rate = number of deaths caused by occupational injuries × 1,000,000 ÷ total working hours.
- Serious occupational injury rate = Number of serious occupational injuries × 1,000,000 ÷ total working hours.
- Total Recordable Injury Frequency Rate (TRIFR) = Total number of recordable occupational injuries
(including serious occupational injuries, deaths, and other recordableoccupational injuries) × 1,000,000 ÷ total working hours. - 6 ~ 8 Points Ratio Calculation: calculate to 2 decimal places without rounding up.
- The ratio of 1,000,000 working hours refers to the number of occupational injuries for every 500 full-time workers within a year, assuming that full-time workers work 2,000 hours in a year.
Statistics on the Frequency and Severity of Disabling Injuries among Chemical Workers in Formosa Laboratories in the Past Three Years
Year | Worker Category | Due to disability injury Caused by Disabling injury | Disabling Frequency Rate (FR) | Disabling Severity Rate (SR) | Overall Damage Index (FSI) |
---|---|---|---|---|---|
2020 | Employee | 46.00 | 5.55 | 28.38 | 0.40 |
Non-employee | 0 | 0 | 0 | 0 | |
2021 | Employee | 61.69 | 8.57 | 37.78 | 0.57 |
Non-employee | 0 | 0 | 0 | 0 | |
2022 | Employee | 13.50 | 13.50 | 8.01 | 0.26 |
Non-employee | 0 | 0 | 0 | 0 |
- Occupational injuries refer to accidental injuries that occur while workers are performing their duties or in the workplace. The statistical criteria do not include commuting 1. Loss of working days: the number of hours unable to work divided by 8 hours is calculated; the calculation is based on occupational injury sick leave (including ≤1 hour), excluding sick leave and menstrual leave.
- Disabling Frequency Rate (FR) = number of disabling injuries × 1,000,000 ÷ total working hours (calculated to 2 decimal places, without rounding)
- Disabling Severity Rate (SR) = number of days lost to disabling injuries in × 1,000,000 ÷ total working hours (calculated to 2 decimal places, without rounding)
- Frequency-Severity Indicator (FSI) = √[(FR × SR) ÷ 1,000] (calculated to the second decimal place, with the third place rounded up)
Health Examination
Formosa Laboratories has long been committed to promoting a healthy workplace environment and protecting the physical and mental health of workers. Every year, regular health examinations are conducted for all employees, including general health examinations and special health examinations for workers engaged in hazardous operation. These special health examinations assess exposure to noise, dimethylformamide, hexane, benzene, chromic acid and its salts, and formaldehyde, which are classified according to the law for health management. The plant nurse and occupational medicine specialists track and provide health education based on the results of the physical exams. If necessary, on-site assessments for suspected work-related illnesses can be conducted. Individuals classified as level three or above in the special health management grading system will be continuously monitored and reclassified. Managers classified as level four will implement measures to control work hazards and seek health consultations and guidance from the health center's professional physicians to ensure that employees do not develop occupational diseases.
According to the statistics of the health management classification in the past three years, as of the end of 2022, there were a total of 5 fourth-level health managers in the Company who had abnormal physical examinations due to special operations. They have all undergone operational hazard control (hearing protection plan) and control measures (controlling exposure time or transferring from the operation). There have been no cases of occupational diseases in the past three years.
Special health examination classification in the past 3 years
Year | Total number of people tested | First-level health manager | Second-level health manager | Third-level health manager | Fourth-level health manager |
---|---|---|---|---|---|
2020 年 | 349 | 275 | 74 | 0 | 0 |
2021 年 | 295 | 238 | 56 | 0 | 1(噪音) |
2022 年 | 241 | 183 | 54 | 0 | 4(噪音) |
Note:
- Level 1 management: Individuals who have been determined to have no abnormalities based on the consolidated results of the examinations.
- Level 2 management: Individuals who have been determined to have abnormalities that are not work-related based on the consolidated results of the examinations.
- Level 3 management: Individuals who have been determined to have abnormalities based on the consolidated results of the examinations, but job relevance cannot be determined and need to be rearranged for an assessment by an occupational medicine specialist.
- Level 4 management: Individuals who have been determined to have abnormalities that are work-related based on the consolidated results of the examinations.